Costa Mesa, CA – Burns Stainless, the renowned name in exhaust engineering, is proud to announce a series of articles on Welding Exhaust Systems. This five-part series, which has been a valuable resource for both new and experienced welders, is packed with handy tips and techniques.
Part 1: We start off with the basics of welding tech, breaking down the differences between TIG and MIG welding. For example, MIG welding is great for automation and is often used in production exhaust systems.
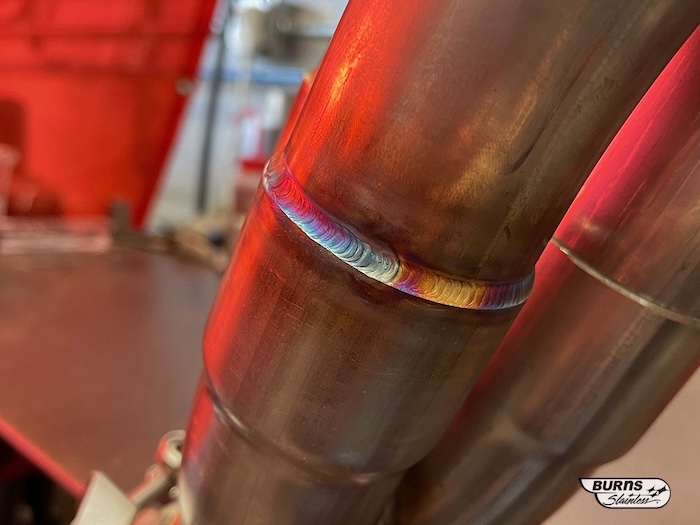
Part 2: Next, we dive into welding thin-walled tubing for racing. When working with thin sections of stainless-steel tubing, like those in racing exhaust headers, it’s crucial to prepare the joints properly.
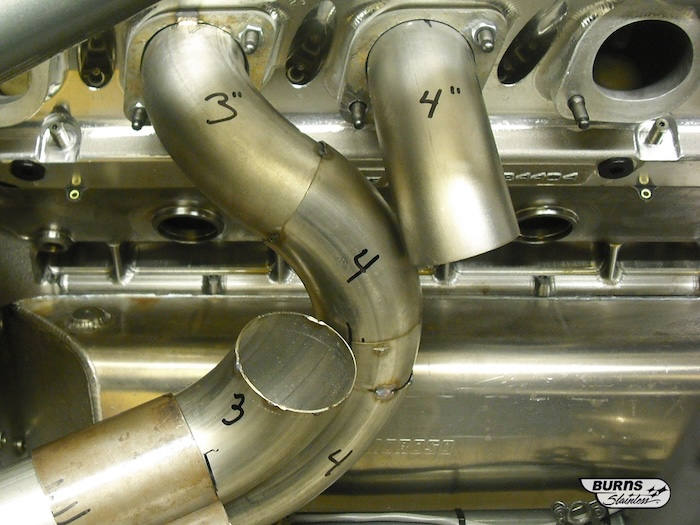
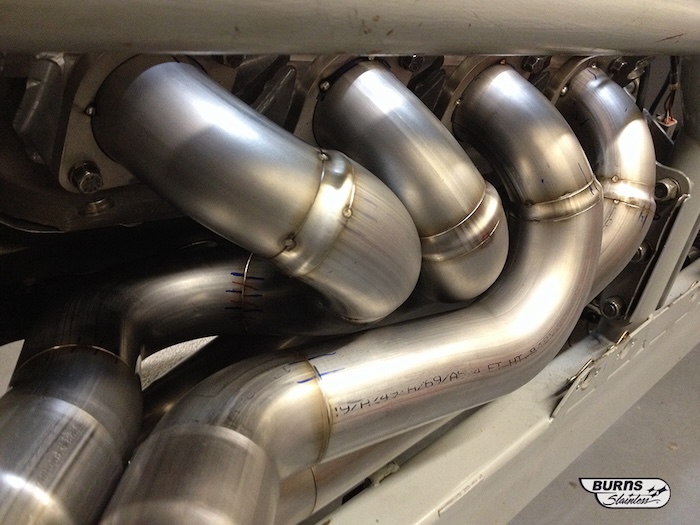
Part 3: In this part, we tackle a topic often missed by newbies: back purging. When welding at high temps, materials like stainless steel and Inconel can form oxides (sugaring or noogies), if not protected from oxygen, leading to a poor weld.
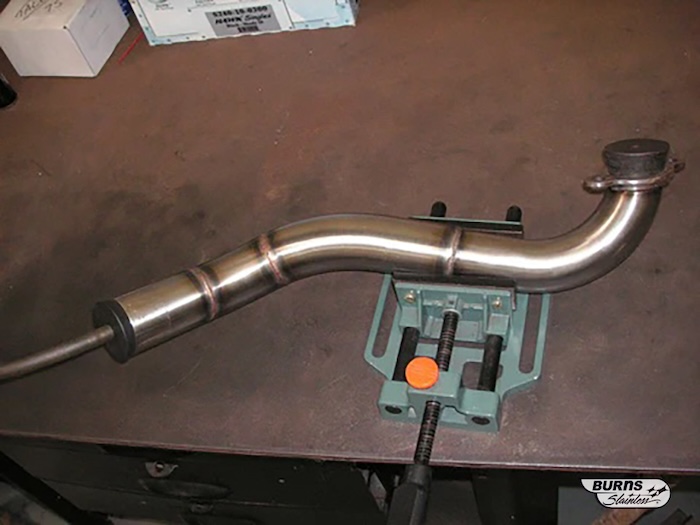
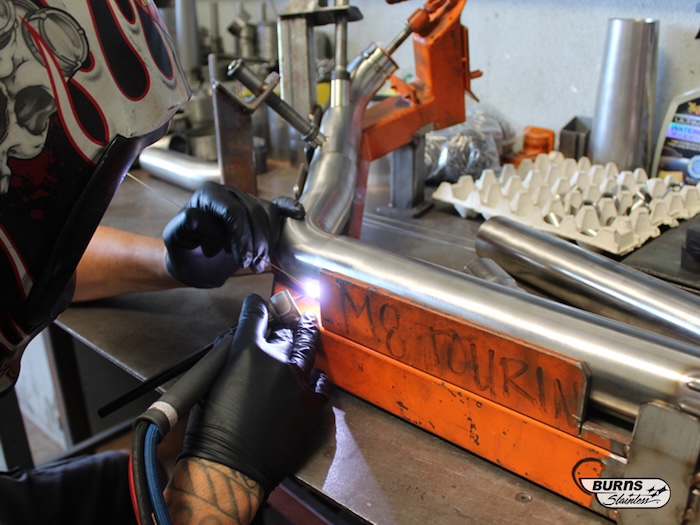
Part 4: Here, we cover the critical flange/exhaust port interface. Ensuring the exhaust pipe is either “port-fit” or just a bit larger (no more than 0.030 inches) than the exhaust port is key for proper flow.

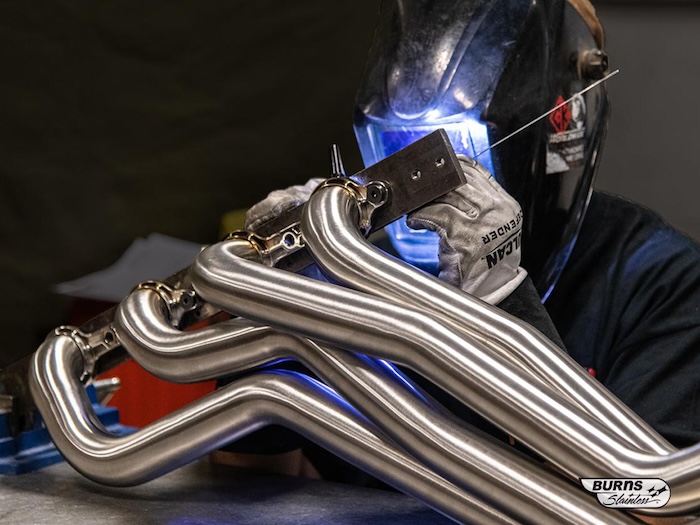
Part 5: We wrap up the series and ready to weld. We’ll talk about essential PPE like gloves and a good welding helmet and share unique tips on the welding process such as keeping a constant speed.
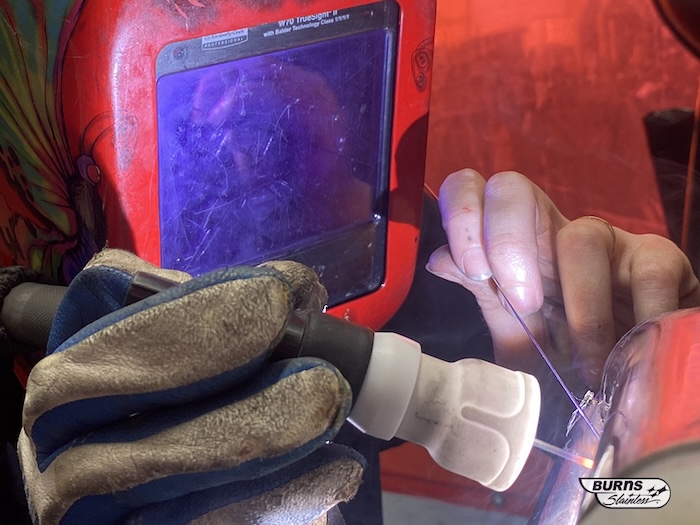
The Burns Stainless Blog offers tips and tech on welding and exhaust design as well as inspirational articles on the people, events, and culture of motorsports. We invite you to take a stroll over to Burns Stainless for more details.